Field Ready uses 3D printing for metal casting
- Field Ready
- Jul 15, 2016
- 2 min read
Field Ready has been working closely with local innovator Madhukar KC on his improved cookstove design. It has been a great way to demonstrate one of the more powerful ways in which an off the shelf FDM 3D printer can be used: as a tool for metal casting.
Madhukar KC has spent ten years iterating his design, and he has focused his attention specifically on designing a better burner to get more oxygen to the wood so it burns more efficiently. For years, he has made his designs out of wood using the tools he had available. He then hands this wooden pattern to a sand casting manufacturer, who uses it to create a sand mould into which molten iron can be poured. The result is a metal casting of his original wooden pattern, ready to be installed in a stove.
However, as his ideas have got more advanced, the tools he has available are no longer advanced enough to realise the complexity of the design ideas. Fortunately, 3D printing a pattern is an easy solution to this problem; Field Ready engineer Ram Chandra Thapa spent time with Madhukar, developing Madhukar’s design as a 3D computer model. The design was then printed and taken to the sand casting foundry, where it was cast in aluminium and cast iron.
The results were brilliant – the new burner design was tested in a customer’s home against the previous design, with the wood burning significantly hotter with the newest design.
The potential of this kind of process is significant for making things in the field – it opens up the possibility of making tools such as hammers, spanners and chisels, or even simple car parts. Even better, small metal foundries are not uncommon in Nepal, so local businesses can be supported in the process. For emergencies where manufacturing capacities have been destroyed, a rapidly deployable iron foundry may become a fundamental piece of kit.

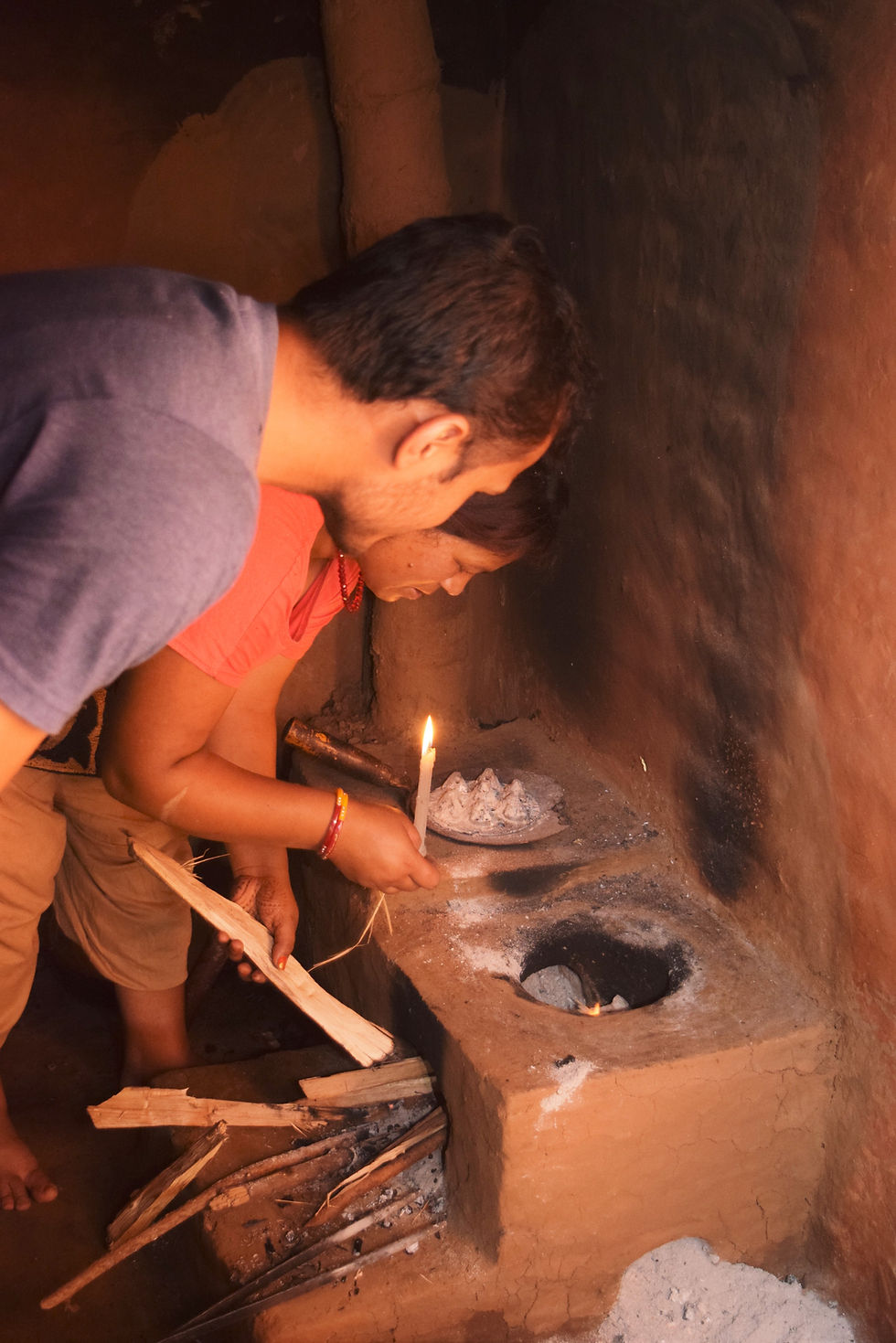

